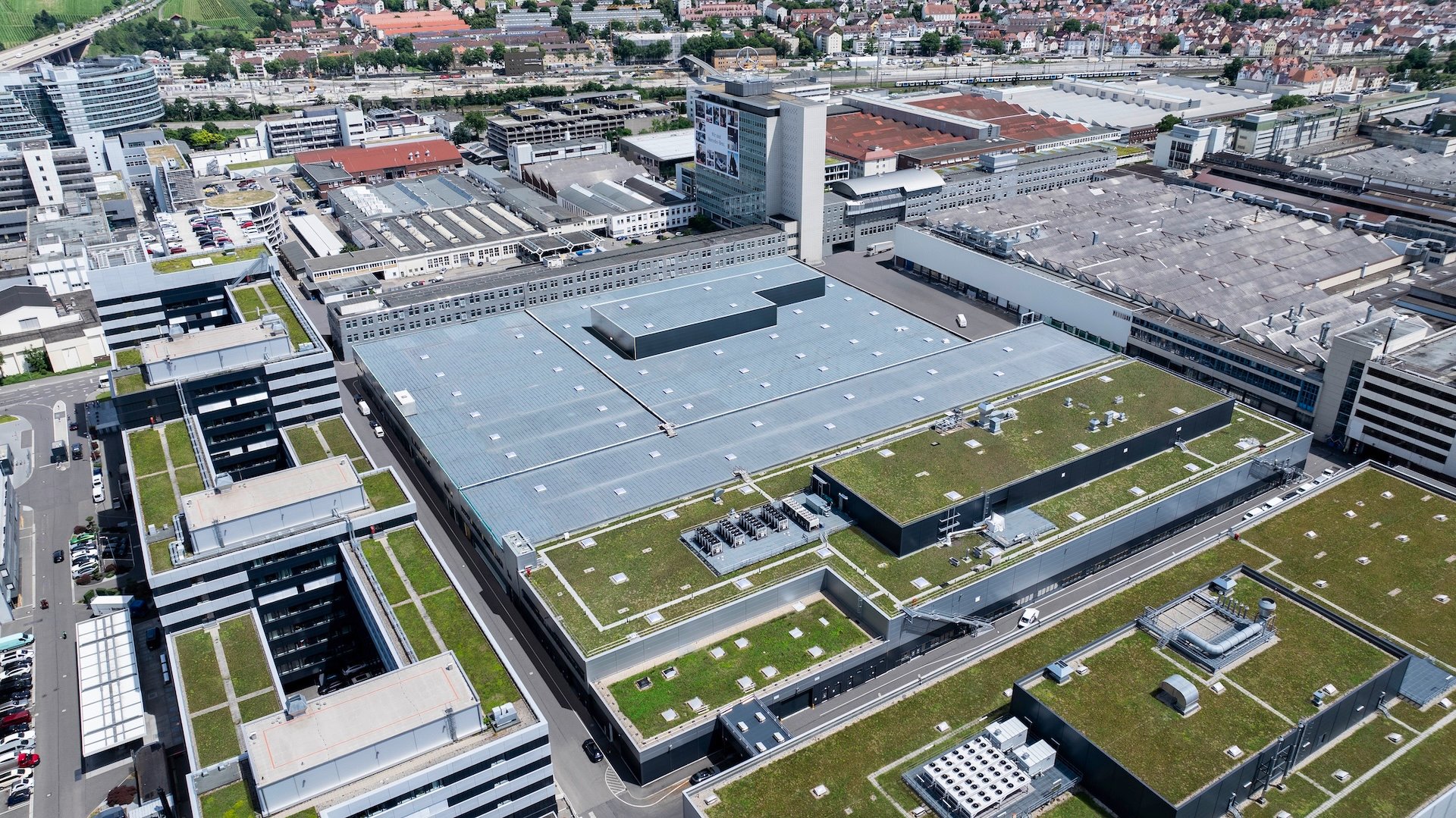
Mercedes‑Benz opened the eCampus at the heart of its headquarters in Stuttgart-Untertürkheim. It is the competence centre for the development of cells and batteries for the future electric vehicles of the brand with the star. Mercedes-Benz is significantly strengthening its development activities in battery technology.
The aim is to develop innovative chemical compositions and optimised production processes for high-performance cells with “Mercedes-Benz DNA” and reduce battery costs by more than 30 percent in the coming years. The Mercedes-Benz eCampus covers the entire field of battery and cell technology. It ranges from the development and evaluation of new cell chemistries and industrial-scale cell production to the testing and certification of complete battery units.
Mercedes-Benz eCampus: concentrated expertise in battery technologies with “Mercedes-Benz DNA”
Mercedes-Benz is developing various forms of cell chemistry. Among other things, the company is working on lithium-ion cells with high-energy anodes based on silicon composites and innovative cobalt-free cathode chemistries, as well as on solid-state battery technology.
Operations at the new competence centre for battery technologies in the heart of the Stuttgart-Untertürkheim plant will start in two stages. The approximately 10,000-square-metre factory for the industrial production of battery cells has started operations after a construction period of around two years. State-of-the-art production facilities in the “Industrial Cell Lab” make it possible to manufacture and test battery cells with different chemistries on an industrial scale. Several tens of thousands of cells can be produced here every year for the development of future battery generations.
The new building for the second stage is due to be completed by the end of this year. Among other things, this state-of-the-art test and proving centre will house a battery ramp-up factory for product and process development as well as maturity assurance for large-scale industrial production. Various functions of the test centre at the Nabern site will be transferred to the eCampus in Untertürkheim for this purpose. State-of-the-art test benches are being built on an area of around 20,000 square metres to comprehensively test and prove the safety and service life of batteries.
120 years of Mercedes-Benz Untertürkheim
With the new eCampus, Mercedes-Benz is consolidating the role of the largest powertrain facility within its global network, which is celebrating its 120th anniversary this year. Investments in the three-digit million-euro range will strengthen Untertürkheim’s role as a high-tech facility for drive technologies – a clear commitment to the workforce and to Baden-Württemberg as a centre of automotive competence.
Founded in 1904, the Mercedes-Benz Stuttgart-Untertürkheim plant spans several sub-sites in the Neckar valley and set the course for e-mobility some time ago.
Since 2022, the Brühl plant has been home to a battery factory producing systems for Mercedes-Benz plug-in hybrid models. The ramp-up of production for batteries for all-electric models starts here in 2024.
Closing the battery loop
The opening of the eCampus marks an important step in Mercedes-Benz’s sustainable business strategy. By 2039, the company aims for its fleet of new vehicles to be net carbon neutral over their entire lifecycle. In addition to decarbonisation, one of the most important levers for this is the establishment of a truly circular economy in order to conserve primary resources. Mercedes-Benz is pursuing a holistic approach to batteries, focussing on three core issues: circular design, value retention and closing the loop.
The company offers reconditioned batteries as spare parts for all electric vehicles in line with the concept of a circular economy and to conserve resources. In addition, the subsidiary Mercedes-Benz Energy has established a successful business model for large-scale stationary storage applications. Batteries that can no longer be used in the vehicle can be reused in second-life storage systems. Material recycling comes at the end of a battery’s life and is the key to closing the materials loop. An important step in this direction is the opening of a battery recycling factory this year in Kuppenheim in southern Germany.
eCampus with sustainable building concept
The building concept for the new eCampus in Stuttgart-Untertürkheim, which covers more than 30,000 square metres, also meets Mercedes-Benz’s sustainability criteria. Its foundations contain recycled concrete made from demolition materials. More than 75 percent of the usable roof area of the state-of-the-art test and proving centre is equipped with photovoltaic systems and supply the facilities with renewable energy. The entire roof area is also being greened. Reversible heat pumps and cold accumulators enable a sustainable heat supply and air conditioning for the hall. Hybrid cooling towers increase the efficiency of the water supply. The goal for all Mercedes-Benz production plants worldwide is to operate with 100 percent renewable energy by 2039.
Statements from the opening of the Mercedes-Benz eCampus
“The opening of the Mercedes-Benz eCampus marks an important step in our sustainable business strategy. It is our ambition to also play a leading technological role in electric mobility. The eCampus brings us closer to this goal. The work carried out here will help to reduce battery costs by more than 30 percent in the coming years. By locating the eCampus at the heart of our centre for research and development of drive systems, it signifies a clear commitment to a more sustainable future and to the long heritage of our Stuttgart-Untertürkheim location.”
Ola Källenius, Chairman of the Board of Management of Mercedes-Benz Group AG
“High-performance batteries comprise the heart of the electrification of transport – and are the key to the successful transformation of the automotive industry. The demand for innovative and sustainable batteries will continue to rise sharply in Europe in the coming years. It is therefore of central importance that Germany and Europe build up their own capacities and, in particular, their own expertise in this key technology. This not only strengthens the industrial location and creates modern, future-proof jobs, but also increases Europe’s resilience. I am delighted that with the new eCampus, Mercedes-Benz will be focusing its research and development activities for batteries at the Untertürkheim site in future. Thereby making an important contribution to the further development of battery technology and the establishment of a strong battery ecosystem in Germany.”
Robert Habeck, German Federal Minister for Economic Affairs and Climate Action
“For me, the Mercedes-Benz main plant in Untertürkheim is associated with the Swabian spirit of innovation, tinkering and invention. It is fantastic that Mercedes-Benz is setting the right course at this place of inspiration with the new eCampus. The Mercedes star shall continue to shine out into the world from Stuttgart in the future.”
Frank Nopper, Mayor of the City of Stuttgart
Source: automotiveworld.com/news