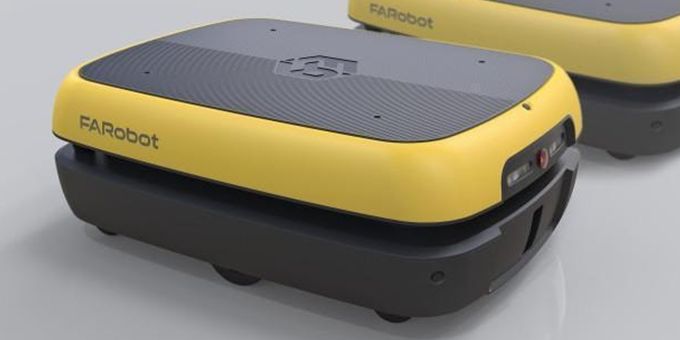
The world is quickly changing for modern warehouses. E-commerce companies, retailers, hospitals, and other third-party logistics businesses view autonomous mobile robots (AMRs) as a critical technology to rein in high labor costs and increase throughput to reduce fulfillment time. Factory owners and managers want quick AMRs that are easy to deploy with the ability to be modified on the fly. Unlike its predecessor, the automated guided vehicle (AGV), an AMR can understand commands and dynamically detect and avoid obstacles to navigate through different work environments without being on a direct path or having an operator control its movement. This article describes developing and deploying AMRs with integrated hardware and software technology, and includes use cases for factories, smart cities, and hospitals.
Sophisticated warehouse demands drive the megatrend from AGV to AMR
The AMR market is booming. In 2020, the market size was $356 million. MarketWatch predicts that it will grow at a compound annual growth rate (CAGR) of 15.9% to $1011 million by 2026. Manufacturing and logistics enterprises' demand high throughput, quick and easy robot deployment, and flexible production lines. This trend, accompanied by the emergence of new applications, is driving a major movement from automated guided vehicles (AGVs) to AMRs. To understand the megatrend from AGVs to AMRs, let’s examine the two technologies.
Automated Guided Vehicle (AGV) vs. Autonomous Mobile Robot (AMR) - Key Differentiators
Until recently, AGVs represented the latest advanced technology – capable of transporting raw materials, works-in-process, and finished goods to manufacturing production lines or storing and retrieving goods in warehouses and logistics centers. AGVs use a combination of software and sensor-based guidance systems to direct their movement. They are safe and reliable at moving loads because they follow a fixed path with precisely controlled acceleration and deceleration and obstacle detection bumpers.
However, AGVs lack flexibility, (see figure 1). If a production line layout changes, for example, this means that the guidance track infrastructure will need rerouting, which often involves time and money. When an AGV detects an obstacle, it stops until someone manually removes the item. Furthermore, AGVs cannot interact with humans because the fleet management system is centralized without peer-to-peer communication.
Figure 1. Comparison between AVGs and AMRs
AMRs are far more flexible. If an operational layout changes, simultaneous localization and mapping (SLAM) let the robot explore the unknown space to create a map automatically without extra effort or cost to the operator. AMRs can use an array of sensor technologies to detect and avoid obstacles dynamically, including people. These robots use sensors and a combination of camera detection and real-time communication technologies, enabling real-time collaboration with humans.
ADLINK and Foxconn form FARobot® for swarm autonomy
ADLINK is currently working with global manufacturing giant, Hon Hai Technology Group (Foxconn). Foxconn used AGVs in their production facilities but they wanted to improve the flexibility of their production lines. Foxconn formed a joint venture with ADLINK, called FARobot®, to develop advanced swarm robot system (SRS) and autonomous mobile robot (AMR) solutions using ROS 2 (Robotic Operating System update that takes ROS 1 out of academia and into the industrial realm).
As AMRs communicate with each other in real-time, they can perform task scheduling and assignment and use peer-to-peer communication to determine the location path for each ARM. If there is a fault in one of the AMRs, the fleet will initiate a backup immediately and automatically send the most suitable robot to assist.
FARobot’s unique AMR solution features swarm collaboration, task failover, and performance optimization. By adopting the latest swarm autonomy technology, a FARobot AMR robot can boost industrial efficiency and productivity - for example, delivering the right raw material or components to the right place at the right time to reduce unnecessary hold-ups.
Source: roboticstomorrow.com