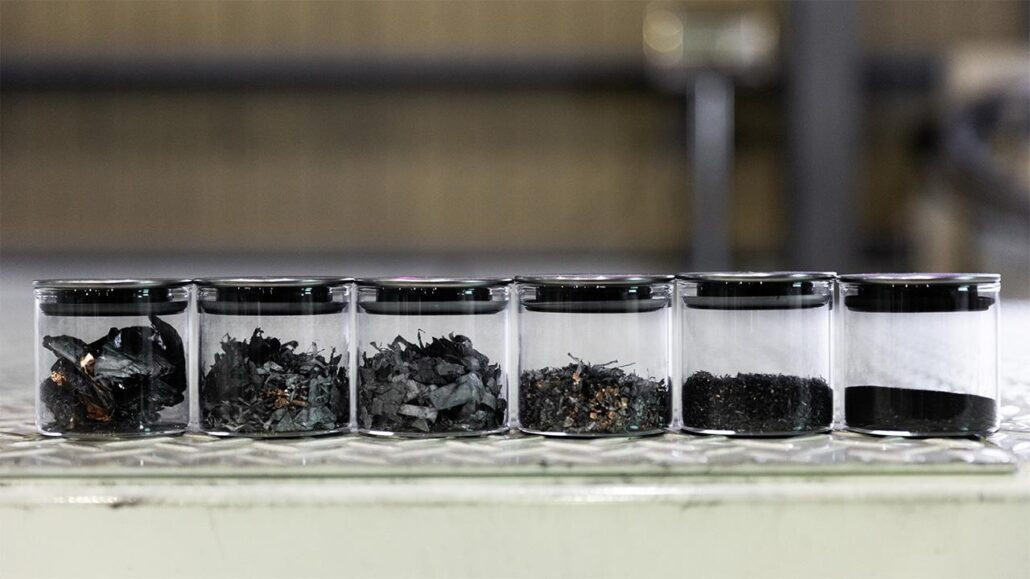
Conventional recycling methods rely on thermal pre-treatment, which involves burning parts of the batteries. This results in carbon emissions and some of the valuable materials being lost. Toyota Chemical Engineering is working on an alternative process for recycling high-voltage (HV) batteries that does not require the conventional incineration process. The goal is to reduce material losses and emissions during recycling. From 2031, battery manufacturers in the EU will be required to use a certain percentage of recycled metals. As a result, the search is on for processes which enable higher recovery rates.
Toyota Chemical Engineeringʼs new process employs mechanical treatment of used batteries. The electrolyte fluid, which is important for ion transport, is distilled and extracted to reduce the risk of fire. The battery cells are then shredded, sorted, and prepared for further processing. The recovered materials, including metal fractions and black mass, are to be delivered to partner companies for further processing. Since 2010, the company has already operated a recycling plant for nickel-metal hydride batteries in Japan using the conventional incineration method.
Source: toyota-media.de