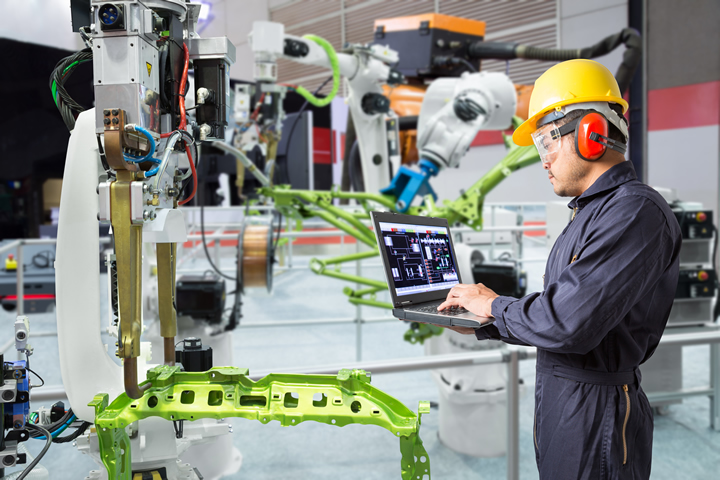
The manufacturing industry is undergoing significant changes due to the swift advancement of technology and evolving global dynamics. With the industry still recovering, manufacturers are searching for ways to strengthen their business resilience and shield themselves from further external economic shocks. Luke Smoothy, Founder and Director of UK-based manufacturing specialist Get It Made, examines the top five trends predicted to influence the manufacturing sector in 2024.
Supply chain digitalization
In an era where supply chain disruptions occur globally, in 2024 manufacturers need to proactively embrace automation and IoT technology to prosper. These developments could improve supply chain fraud prevention, waste reduction, and operational efficiency. Additionally, in order to quickly respond to disruptions, manufacturers need to invest in technology solutions that give them complete visibility and control over their supply chain. To do this, they need to use data-driven inventory management to find hidden inefficiencies in their supply chain. This will help them respond to changes in the supply chain environment and minimise disruptions. In addition, while maintaining value, manufacturers should look for creative ways to add flexibility and boost dependability in their supply chain.
Sustainability and cleaner energy
Businesses in all sectors, including manufacturing, must work to lessen their carbon footprint and emissions. To do this, manufacturers need to move away from fossil fuels and towards renewable energy sources to accelerate the process of reaching net zero emissions. Furthermore, manufacturers need to demonstrate that they can track the origin of each component in their products as the concept of traceability becomes more and more popular. More investments need to be made in data management systems and technology which enable real-time tracking and reporting so as to fully capitalise on the traceability trend. What’s more, manufacturers working with vendors who are equally dedicated to openness and ethical behaviour will help reshape the industry and steer it in the direction of sustainability and social responsibility.
Smart factories – IoT and automation
For manufacturers who embrace automation to create smart factories in 2024, the future is bright. Automation of key manufacturing processes delivers a competitive advantage for manufacturers struggling to combat rising costs and disruptions in the supply chain. The performance gap between manufacturers who have embraced digital transformation and cloud adoption and those who have not will continue to grow as the business environment becomes more complex.
Industry 4.0, or smart manufacturing, holds great promise if manufacturers can streamline workflows, collect accurate, real-time financial and production data, as well as reduce costs. More manufacturers need to look at incorporating smart technology in order to achieve this and seize the benefits from lower operating costs and increased efficiency. To fully embrace the smart factory revolution, using data for improved forecasting, predictive maintenance, and shortage or bottleneck identification is pivotal. The advantages of smart factory software and aftermarket sensors are becoming increasingly apparent as their costs continue to drop. In a smart factory setting, more manufacturers must gravitate towards implementing digital twin technology to assess product dimensions, simulate variations in supply and demand, and make well-informed decisions.
Predictive resolution
By 2030, the global predictive market is expected to grow rapidly. By 2030, it is expected to have grown from its modest $4.5 billion valuation in 2020 to a staggering $64 billion. This suggests that predictive analytics and related technologies are growing in prominence in the manufacturing sector. For years, manufacturers have been waiting impatiently for predictive resolution, but data issues have prevented them.
Manufacturers can now transform massive amounts of unstructured data, including Word and PDF files, into useful predictive insights with the help of AI, machine learning, and natural language processing. A predictive resolution will pave the way for a manufacturing revolution that will bring about cost savings, increased efficiency, and exceptional predictive ability.
It is now essential to adopt predictive resolution in the world of fast-paced manufacturing. It should be used by contemporary companies to solve issues such as the requirement to decrease downtime, increase equipment longevity, and guarantee client satisfaction. In order to anticipate problems before they cause expensive disruptions, manufacturers should incorporate predictive resolution with IIoT. As a result, they would benefit from improved customer satisfaction, fewer downtimes, and more seamless operations. But to bring about genuinely revolutionary change, moving forwards manufacturers must also take advantage of predictive resolution's ability to enhance data analytics and real-time monitoring.
Building and upskilling
Although manufacturers have made strides in modifying their workforce policies to enhance the attraction and retention of talent, further approaches may be taken into consideration in 2024 to maintain this momentum. One possible hiring strategy is to build and upskill the talent pipeline. Manufacturers can foster local talent, mentor students, and create future pipelines of STEM-ready workers by collaborating with educational institutions that begin preparing students for STEM careers as early as primary school. This is a strategic approach for both community involvement and long-term talent attraction and retention. Establishing a relationship with community and technical colleges can facilitate the integration of industry knowledge and innovative educational practises, thereby equipping students with targeted skills.
Additionally, manufacturers ought to consider how to develop fresh avenues for retraining staff. Businesses might, for instance, adopt automation and digitization to free up three extra hours per day per employee, and then use those extra hours to provide more training sessions to them. This could help manufacturers create career pathways and better prepare staff for jobs of both the present and the future, including those requiring advanced digital skills. The industrial metaverse can also be used to provide innovative, effective, improved, and adaptable training techniques which are accessible remotely.
Future adoption
These developments signify a significant shift in the way today’s manufacturing is done. Success in 2024 and beyond will depend on how well manufacturers accept these changes and how receptive they are to new ideas, in order to maintain a competitive edge.
Source: roboticstomorrow.com