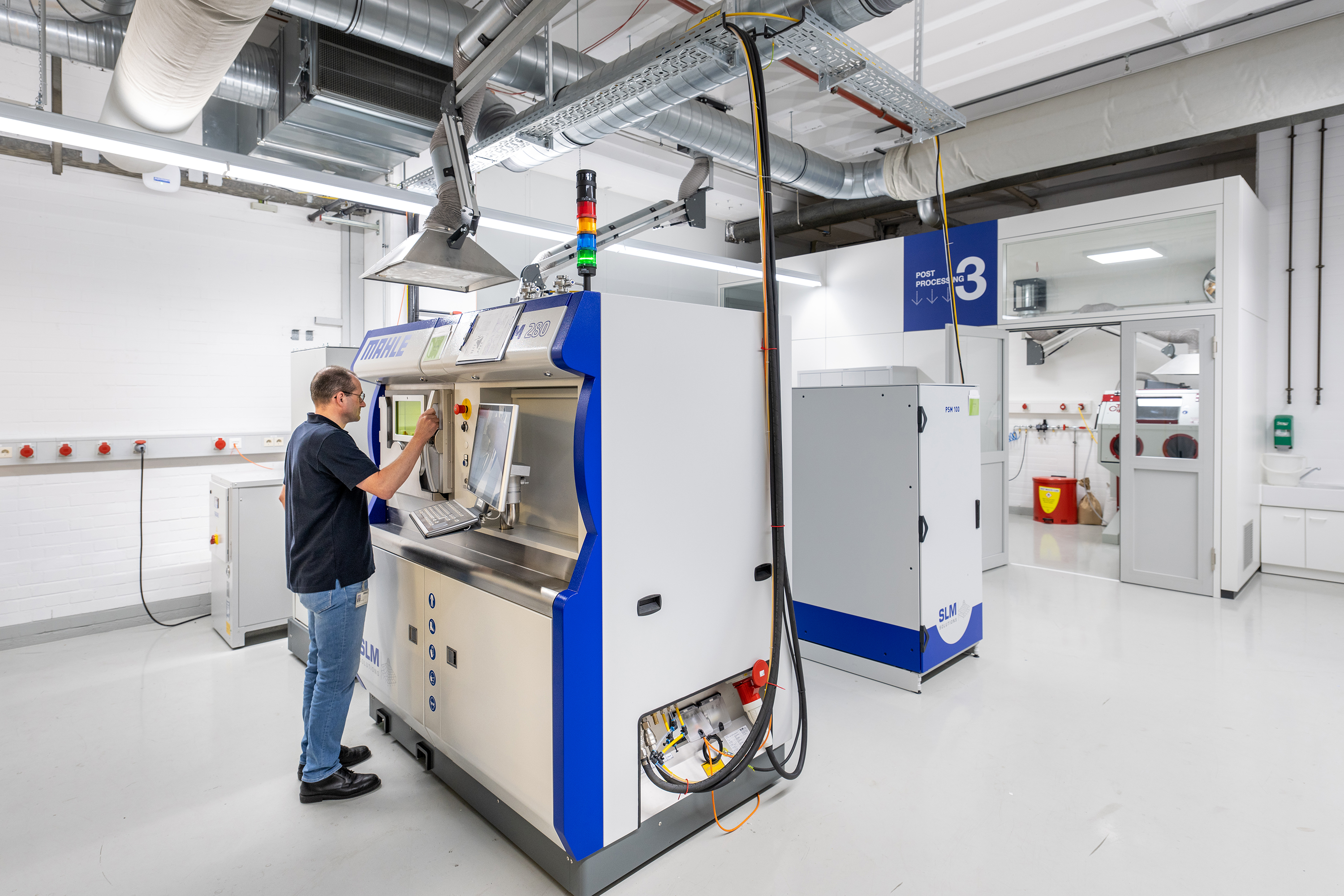
- New MAHLE 3D printing center in Stuttgart strengthens MAHLE’s role as a leading development partner to the automotive industry
- Prototype production in the future will take only a few days instead of several months
- New center accelerates development of climate-neutral drive technologies at MAHLE
- Further focus on the development of 3D printing processes for industrial series production
MAHLE is pushing ahead with 3D printing. The technology group has opened a new center for additive manufacturing processes at its headquarters in Stuttgart. In the future, MAHLE will be able to shorten the time it takes to produce prototypes for complex components from several months to just a few days. This will also significantly accelerate the development of climate-neutral drive technologies, for example, for e-mobility. In doing so, MAHLE is strengthening its role as a leading development partner to the automotive industry. The 3D printing center, which houses the printers, powder preparation module, testing laboratory, and a blasting system for finish machining the components, is also used for internal prototype production as well as for customer orders.
“The development of new systems and components has to be much faster today than it was a few years ago, especially when it comes to solutions for sustainable CO2-neutral drive systems,” says Michael Frick, Chairman of the MAHLE Management Board (ad interim) and CFO. “With our new 3D printing center, MAHLE is once again stepping up the pace in its strategic fields, for example E-mobility.”
Dr. Martin Berger, Head of Corporate Research and Advanced Engineering at MAHLE, points out: “Processes are also being developed in the new center that enable 3D printing in industrial series production based on the strict standards of the automotive industry. This opens up completely new possibilities in product development and manufacturing, because these processes can be used to produce high-performance components that cannot be manufactured using conventional methods.” MAHLE’s broad expertise in materials guarantees the production of extremely high-performance components that can withstand even extreme loads. MAHLE has already proven the performance of parts produced in this way in a joint project with Porsche and Trumpf in which high-performance parts such as pistons and charge air coolers for the Porsche 911 GT2 RS super sports car were successfully produced and tested. The main advantages of the process were the elimination of the need for expensive production tools and the ability to create complex structures that could not be produced using conventional methods. The focus of the newly opened 3D printing center is on components from the fields of thermal management, mechatronics, and electronics for which manufacturing processes are developed and qualified for subsequent series production. The materials used are special aluminum and stainless steel alloys which, depending on the intended use, are particularly resilient, corrosion-resistant, or weight-optimized.
Source: mahle.com/en/news-and-press/press-releases