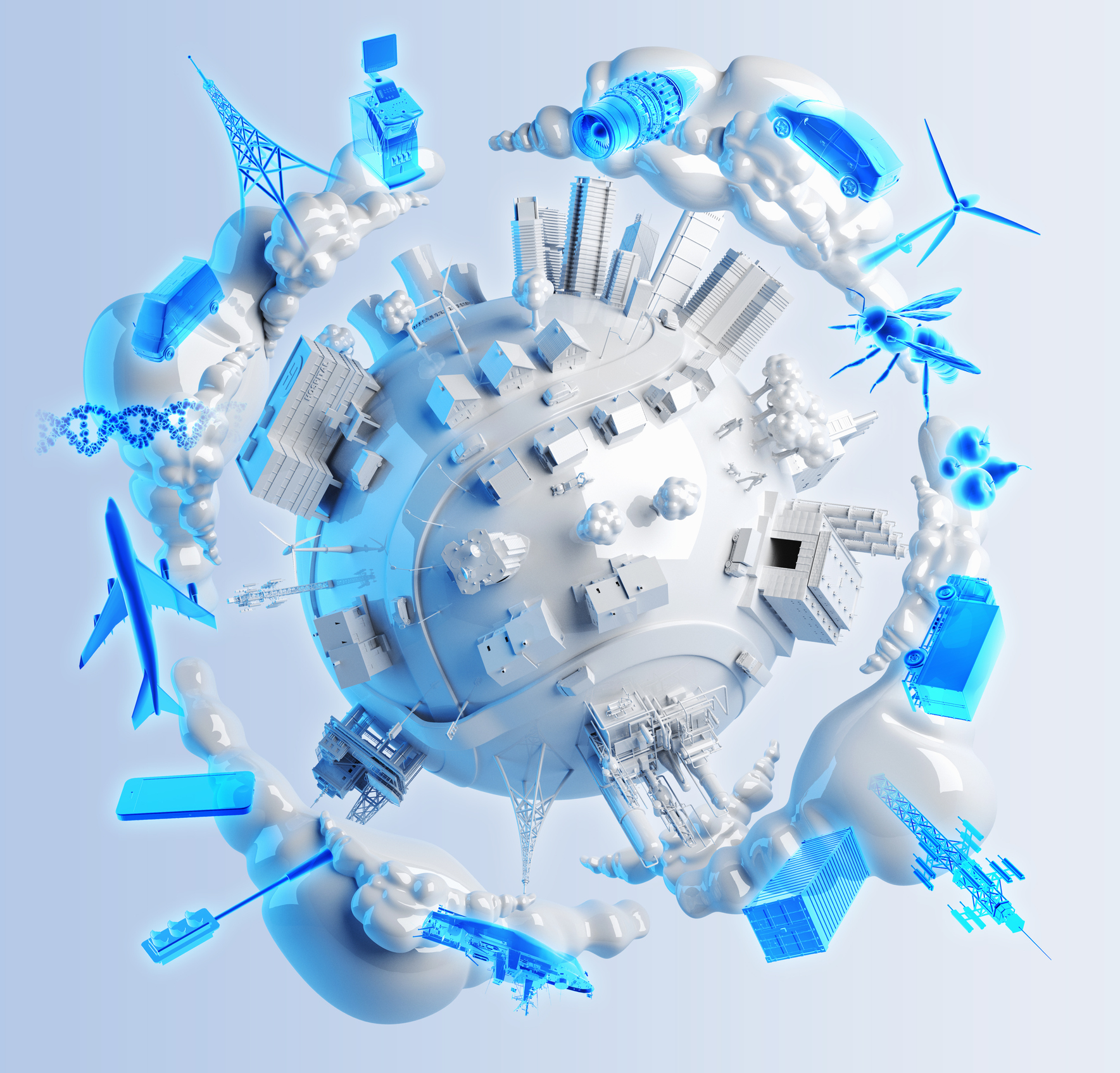
It’s often and comprehensively reported that we’re hurtling towards the fourth Industrial Revolution, the Factory of the Future or Industry 4.0, as the Europeans call it. But are we really ready for it?
The manufacturing industry has talked Lean for years; the principles and the methodology are well known and established.
Lean manufacturing, or smart manufacturing, is as valid today as it ever has been. How can a process that eliminates waste and increases resource utilization and productivity become outdated? OEE (Overall equipment effectiveness) matters! These are business critical issues and always will be.
However, the theory of Lean, and how it is put into practice is evolving. Necessarily so, as manufacturers strive to remain competitive in an industry where new technologies are opening up advanced opportunities.
We’ve found that although there is a broad, and in some cases deep, understanding of Lean principles, many manufacturers are still not harnessing its true benefits, because principles don’t necessarily translate to practice.
Because most companies take a project approach, the model is not embraced effectively and lean opportunities cannot reach their full potential. A deep understanding of the theory and the implementation of a process of continuous improvement is essential and will become more so as the manufacturing environment continue to evolve.
Future fit
More than ever, manufacturers need to recognize the need for change before it’s too late. Customer requirements and business models are evolving rapidly, and knowing what they will demand in the future should, as always, dictate business strategy. However, this means more than just knowing the product they’ll want. This means knowing how they want to access, market and use the products.
This is one of the most significant changes of the last decade. It’s clear to see when looking at new, up and coming companies, which are overtaking established incumbents at an alarming rate. Many have one common denominator: access over ownership. Traditional players must evolve to remain relevant.
Information is the new business currency. Across the enterprise, down to the shop floor, it must be easily accessed, easily updated and easily evaluated to enable quick decision making, action and, ultimately, the flexibility companies will need to evolve and thrive.
Well segmented, actionable data allows manufacturers to identify and react to changes in customer bases, to ensure rapid evaluation of options and efficiency of value proposition delivery. Most of all, it enables flexibility to respond quickly, open new customer experiences and enhance existing ones, and drive customer intimacy, for which they will be rewarded.
Barriers to the Factory of the Future
There are multiple barriers to overcome before claiming status as a Factory of the Future, but they can largely be classified into security, standardization and skills.
Security
With more data and devices comes more risk. The IT world is fighting its own battles with regards to information security as data multiplies. This consideration is even more complex when it comes to industrial automation. Cyber-physical security is critical, so security systems need to evolve with the technologies that will shape the Factory of the Future.
Broadly, this will mean moving to virtual security solutions, which can protect both physical and non-physical assets. Security and industrial control systems must be integrated to allow full operational oversight and gap analysis.
Standardization
Standardization is the fundamental principle underpinning the success of the Factory of the Future. It’s the basic premise to ensure that different machines, operators, and analysts are all talking the same language. It forms the basis for communication between production, automation and oversight.
Overall equipment effectiveness (OEE) is still king: measuring availability, performance and quality to make operations faster, cheaper and smarter. With data from the entire factory floor, continuous improvement can be embedded in operations. More than this though, organizations benefit from a clearer understanding of potential step changes, coupled with knowing when and how to implement the critical path elements.
Skills
A unique skillset is required to operate, maintain and secure both industrial and ‘virtual’ machine processes. This skills gap represents one of the biggest challenges on moving to the Factory of the Future.
There are also cultural considerations to overcome in bringing together two distinct ‘legacy’ teams that have traditionally had responsibility for, and expertise in, very different areas. Investment in sourcing talent and training will be critical, to overcome the barriers to the significant opportunities presented by new technologies and the future factory.
The Technology that will Take Us to the Factory of the Future
Although there are barriers to overcome, they are not insurmountable. In practice, there are three key areas to consider in fast forwarding your operations towards the Factory of the Future.
Success is dependent on ‘intelligent machining’: equipment that has dialog with operators and informs strategic decision making. To empower your factory floor, there are three main elements to consider: sensing technologies, software and analytic models, and machine tool health and maintenance.
To empower the factory floor, each of these technologies must continue to evolve to the point at which all variables can be accounted for constantly, in order for the machine tool to make necessary adjustments throughout a given production run.
There are many existing, developing and emerging technologies in each of these areas that will potentially play key enabling roles in changing the current machining paradigm. Many of these will ultimately be incorporated into highly sophisticated intelligent machine tools that will sense current condition and provide machine correction and remediation which takes into account the many dynamics that occur during machining.
Sensing
Touch probes, laser and vision systems utilize metrology and/or optics based technologies to determine tool wear and part quality in line with machining forces.
Tool Data Management (TDM) and Analytics manages and organizes the data for tools, jigs, fixtures and measuring equipment for inventory management and condition monitoring of cutting tools. TDM technology will eventually be incorporated into Manufacturing Execution Systems (MES), which serve as a knowledge base for all information in a facility. Tool condition and production cycle and quality information can be combined to estimate the necessary supply of tooling and ensure an uninterrupted flow in the Factory of the Future.
Tool Condition Monitoring (TCM) monitors the condition of the cutting tools relative to wear, breakage, collision, and availability. In addition, some systems are capable of adaptive control and spindle condition monitoring.
Machine vision inspection is concerned with locating, identifying, measuring, and inspecting manufactured parts. The quality and metrology data is collected from parts either on the shop floor or within a controlled environment of a metrology room. The data can be gathered in the form of a point cloud, magnetic field, or camera link technology. Machine vision provides for a less intrusive inspection (less handling) and less contact with the actual component, leading to higher throughput and higher quality components.
Today, machine vision is commercially available in various non-machining industries and for use outside the actual machine itself. While still evolving for the machining process--there are issues such as coolant mist, chips and other environmental concerns that need to be addressed--these systems could play an important part of any ultimate solution.
In the Factory of the Future, another key enabler will be ‘smart’ inserts and tools. A smart tool or insert is the generic denomination of a cutting insert that has some form of sensing capability, allowing users to monitor the process and/or condition of the cutting tool. These would allow much more accurate control of tool condition and prevention/prediction of tool breakage. This technology is in the early research stage and is not commercially available, but once available it could revolutionize tool condition monitoring and play a key role in the future of machining.
Software and Analytic Models
Most solutions today only address the cutting or grinding process parameters, which only serves as a starting reference point. What is needed in future machining are analytic tools that continually adjust to the current operating conditions. Insight must be acted upon; data must determine decisions and machines must be able to make them.
In common practice, the control mechanisms of a computerized numerically controlled (CNC) machine follows pre-programmed and constant speed and feed-rates for each cutting segment of a given shape. As such, the NC programs cannot take into consideration any dynamic variations encountered during cutting.
A solution to this inflexibility, is to use adaptive control systems which continuously monitor cutting conditions in real time and provide automatic cutting parameters (such as feed or speed) optimization. Adaptive control is often part of tool or machine condition monitoring systems and involves different sensing, data processing, and actuation solutions.
A typical adaptive control system monitors the power or cutting forces of a cut in real time and adjusts the feed rate in order to obtain optimized cutting conditions. Adaptive control technologies are still evolving as new machine tool control, sensors, and concepts continue to develop.
The reality is that the software and analytic models required for a true Factory of the Future will require highly dynamic, multi-objective optimization software. This software will not only need to optimize itself for the given conditions, but also for total cost consideration in order to operate at maximum overall efficiency. This means optimizing to balance cutting speed/feeds versus tooling costs and part quality to provide the best performance and cost against your specific objectives.
Machine Tool Health and Maintenance
Obviously breakdowns in equipment, notwithstanding previously mentioned cutting tool breakage, can jeopardize the Factory of the Future. If your machine breaks, or is not functioning, all the other technologies that make things run, just won’t!
Today’s complex and advanced machining processes demand highly sophisticated and costly maintenance strategies. When you observe that across many industries 15% to 40% of manufacturing costs and machine downtime are typically attributable to maintenance activities, it becomes a real issue.
There are significant technical challenges in machine tool condition monitoring and subsequent maintenance regimes. Current technologies typically ascertain ‘normal’ versus ‘abnormal’ behavior. This works fairly well for primary applications utilizing condition monitoring for equipment operating at constant or near constant loading, for example, hydroelectric, gas and steam turbines for power generation or large compressors. While all relevant, the highly dynamic environment of machining poses real challenges when employing existing technologies.
The issues become evident when trying to identify which component of a subassembly is degrading or failing to the point that the machine tool is becoming either non-operational, or incapable of generating parts within required specifications. Operational safety, maintenance, cost effectiveness, and asset availability have a direct impact, not just on the competitiveness of organizations, but the viability for the Factory of the Future.
Besides maintenance costs, machine availability has a direct impact on organizational agility and efficiency. Unscheduled or frequent breakdowns create significant obstacles to the implementation of modern management strategies, known to improve productivity and reduce production costs. Proper maintenance will result not only in machine uptime and savings in repair costs, but also in an increase in quality of manufactured parts, and in decreasing the costs associated with safety and environmental preservation.
Technologies are still evolving. Monitoring the health of the complex systems that make up the entire machine tool is still in the research and development stages. The evolution of machine-tool health monitoring and management systems will probably become a standard necessity in future.
One of the critical actions manufacturers can implement to make the move to the Factory of the Future, is to avoid doing everything themselves. The most successful companies don’t. They leverage others’ knowledge and expertise, capabilities, assets and channels to bring the best mix together to satisfy customer needs.
Source: industryweek.com