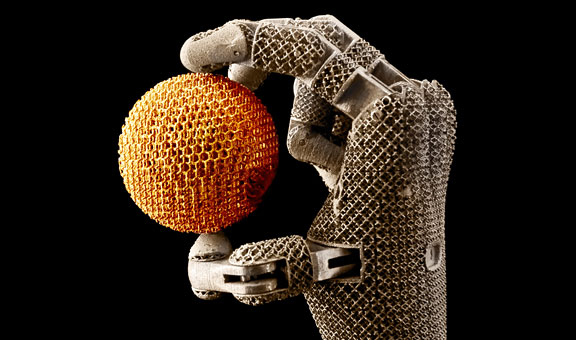
Often considered a “futuristic” technology, industrial 3-D printing (also known as additive manufacturing) is already being implemented in a wide variety of industries, and companies are reaping the benefits.
The process of additive manufacturing involves growing objects layer by layer from a variety of materials, such as plastics or metals. The benefits are widespread, allotting for more design freedom, improving costs when manufacturing small batch sizes and allowing for increased product customization, among others.
Although companies in a wide range of industries, including automotive, tooling, dental, etc., find value in the additive manufacturing process, there are two industries that are positioned particularly well to see growth and success from additive manufacturing: aerospace and medical.
Aerospace Industry
The aerospace industry, one where safety and consistency is not only a priority but a necessity, was quick to adopt additive manufacturing. An industry dependent on advanced research and development, additive manufacturing presented aerospace with a means to easily prototype new products.
However, it doesn’t end there. A study from SmarTech Markets forecasts that the “aerospace industry’s adoption of 3D printing solutions is projected to increase from $723 million in 2015 to $3.45 billion in 2023, attaining a 18.97% compound annual growth rate."
The projected accelerated growth stems from the countless benefits additive manufacturing provides the aerospace industry--including but not limited to cost reduction, lightweight design, and tool-less production.
Leading helicopter manufacturer, Bell Helicopter, used additive manufacturing to prototype a range of different components for their aircraft, but wanted to begin to use the technology for functional parts. With the help of additive manufacturing company, EOS, Bell Helicopter designed and produced flight-certified components for its commercial aircraft.
Bell Helicopter discovered one of the biggest benefits to using this technology: the increased ability to quickly and easily reiterate their new designs. No company gets everything right on the first try, but usually changing the design of a manufactured product involves new molds, new tool paths and a lot of money.
However, changing the design of an additively manufactured component simply requires revising a CAD file, resulting in very little wasted time and money. This, along with the elimination of assembly costs, means that not only can companies manufacture superior products, but they can do so at a lower cost.
Medical Industry
While additive manufacturing can save the aerospace industry time and money, it can also save lives in the medical field. With an expected growth of $2.88 billion from 2015 to 2023 according to SmarTech Markets, the medical industry can expect a future of nano-scale medicine and even complex printed organs. Currently, 3-D printing technology allows for quick and cost-effective production of specialized surgical instruments, medical devices and implants.
Every person is unique and has individualized needs. So when a person was missing a significant portion of cranial bone, Oxford Performance Materials (OPM) turned to additive manufacturing to develop the cranial implant. Using EOS’ machines, OPM created a customized, patient-specific cranial implant--the exact right fit. This meant a shorter surgery, shorter recovery time and lowered risk of infection for the patient. Additionally, this saves the patient money as hospital and operating room rates run upwards of $60 per minute.
And this is just the beginning for additive manufacturing in the medical field. OPM President and CEO, Scott DeFelice, notes “there is no region of the human skeletal anatomy that won’t be touched by this technology.”
Rapid prototyping, hyper-customization and ability to manufacture small batches of product all contribute to the aerospace and medical industries’ quick and accelerating adoption of additive manufacturing. However, the technology provides solutions to companies in industries ranging from consumer and lifestyle to tooling to automotive. The industrial world is only beginning to understand the value of additive manufacturing, and there is no doubt that new applications will continue to be discovered as the technology advances.
One of additive manufacturing’s greatest challenges rests in the mindset of engineers and manufacturers. Before the world sees mass-adoption of the technology, there must be a shift in how we approach design. In the past, production capabilities determined the design of products. Now it is critical to re-train engineers and designers think in terms of design-driven manufacturing--providing high degrees of design freedom. Only once the thought process behind manufacturing changes will additive manufacturing fully reach its potential.
Source: industryweek.com