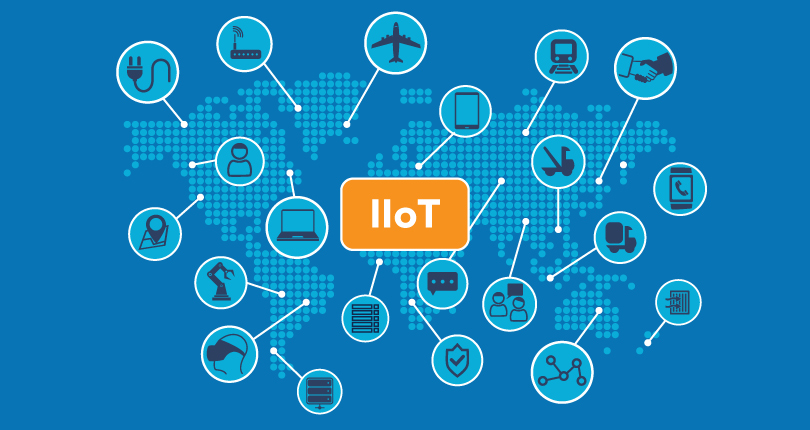
With IIoT and web technology software, the ability for organizations to install, configure and control manufacturing applications from a centralized location is finally a reality.
As manufacturers continue incorporating IoT into their businesses, they are realizing business value by integrating data from enterprise functions – such as product design, supply chain and customer management – with plant-floor production.
In the last few years, manufacturers and industrial organizations around the world are starting to invest in Industrial Internet of Things (IIoT) programs and initiatives to help accelerate the era of IT-optimized smart manufacturing. As IIoT solutions providers better frame, define and create IIoT strategies, many organizations have started to look at what is possible in the age of Industry 4.0 by embracing the Internet of Things and smart manufacturing. In the United States, the number of industrial device-to-device connections is expected to rise to nearly 180 million in 2020 from approximately 50 million in 2014. In China, the rise in machine digitalization is projected to be double that of the U.S. in 2020.
According to Beth Parkinson, market development director for The Connected Enterprise,Rockwell Automation, there are now four key areas that impact IIoT adoption:
Competition – Economic and political factors are putting more competitive pressure on global companies. Business models – including the people, technology and brand proposition – are under close scrutiny to remain relevant for the long term. As industrial organizations converge their IT and OT systems, and build in more flexibility, they can more easily communicate across their enterprises and respond to market changes.
Workforce – Retirement, economic expansion and technology evolution are overwhelming companies’ ability to staff their operations. Tribal knowledge is leaving with the aging workforce, and incoming talent often lacks the necessary technology skills. Companies that take a multifaceted approach – including more intuitive machine designs, IoT-enabling technologies and advanced training – can better prepare their operations and empower employees through the workforce transformations.
Risks – Smart-manufacturing strategies like remote monitoring and BYOD tactics can create security risks. As a result, companies are starting to implement policies to address these concerns, and help maintain and strengthen system security.
Technology – The ability for an organization to collaborate across departments, including design, operation, maintenance and support is becoming more possible through the IIoT. Companies are able to connect many intelligent devices on one standard network, such as Ethernet, which allows them to capture, move and analyze data across an entire enterprise.
Adding to this, Rod Emery, Vice President of Operations, RedViking, emphasizes two more key drivers:
Flexibility – With IIoT and web technology software, the ability for organizations to install, configure and control manufacturing applications from a centralized location is finally a reality. Up until recently, only large industrial organizations could accomplish this. Now, every manufacturer, regardless of size or budget, can embrace digitalization.
Scalability – As scalability has applied to machinery, assembly lines, and conveyance, it now applies to manufacturing software. Software applications can be purchased as manufacturers need them and when production demand requires. Across a broader range of industries different configurations are continuing to expand as manufacturers recognize the value proposition. Strategic IIoT demands that organizations take a fresh look at scalable manufacturing and apply it to equipment that hasn’t traditionally been in the industrial automation mix.
Since the launch of the Industrial Automation North America trade show at IMTS 2012 and its co-location again at IMTS 2014, we have seen rapid technological evolution in the manufacturing industry due to the rise of Industry 4.0 introduced at HANNOVER MESSE in 2013. “This rapid technology evolution has brought us to an inflection point today,” says Parkinson. Companies are realizing business value by integrating data from enterprise functions – such as product design, supply chain and customer management – with plant-floor production.
“To capture this value, companies must adopt certain enabling technologies like smart devices, data analytics, cloud computing and mobility. They can start implementing these technologies by first conducting a baseline assessment to understand key objectives and areas of opportunity before securely upgrading and connecting smarter assets,” adds Parkinson.
Many industrial organizations are buried in data and want to understand how to conduct better analytics to best manage production. Adds Emery, “Today, there is so much activity in the IIoT arena. We are constantly encouraging our clients to investigate intelligent devices. We understand it takes time and careful consideration when driving towards better, smarter manufacturing approaches.”
Digital Factory Is Focal Point of Industrial Automation North America 2016
During HANNOVER MESSE 2016 this April and coming up this September at the Industrial Automation North America trade show at IMTS 2016, visitors will come face-to-face with the most evolved digital factory innovations. Industrial technology exhibitors from around the globe will be emphasizing this need to adopt smart, transportable data and connections onto the plant floor.
Parkinson says, “The powertrain demonstration at the Rockwell Automation booth will showcase integrated PACs from Rockwell Automation with FANUC CNC and robots.”
Rockwell Automation’s demonstration will highlight the safety-signature aggregation capability, which enables an EtherNet/IP network to collect safety signatures from controllers and send alerts when a specific asset requires attention. To showcase how cloud-based data analysis can predict and prevent unexpected downtime from automation equipment, the FANUC robot will be connected to the internet using a connected infrastructure built upon Cisco and Rockwell Automation products.
Visitors to RedViking’s booth will experience the worldwide launch of Argonaut, a manufacturing performance platform and IIoT solution that offers manufacturers the ability to install only the manufacturing apps they need, where they need them, and to control them from a central location.
Emery says, “Security is one of the foundations of Argonaut and its IIoT gateway. Our customers understand this is a cornerstone of adopting IIoT, which will allow them to safely bring more products to the market in a faster timeframe.”
Larry Turner is president/CEO of Hannover Fairs USA, Inc., Deutsche Messe’s U.S. subsidiary and organizer of five co-located Industrial Technology Events at IMTS 2016. Leading smart manufacturing solution providers such as FORCAM, Mitsubishi Electric Automation, System Insights and a host of international connected factory device providers will join Rockwell Automation and RedViking in September at IMTS 2016.
Source: industryweek.com